4 reasons why recuperators are not the best solution for reducing your heat consumption
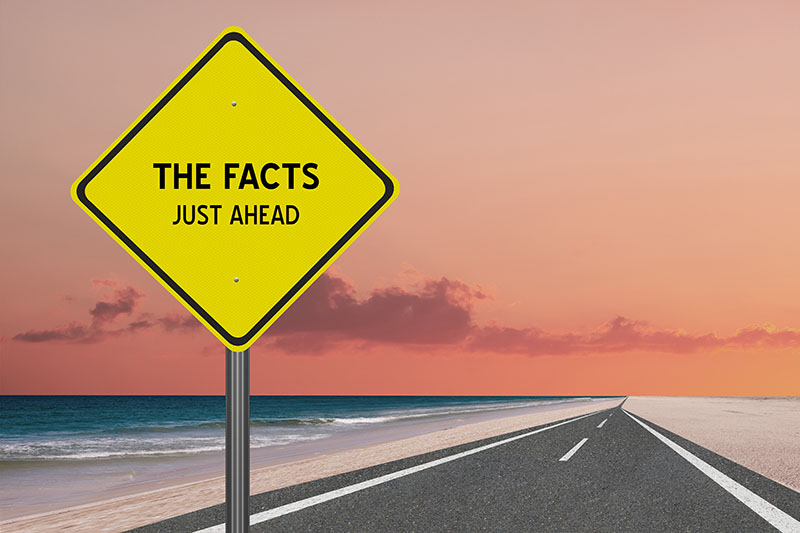
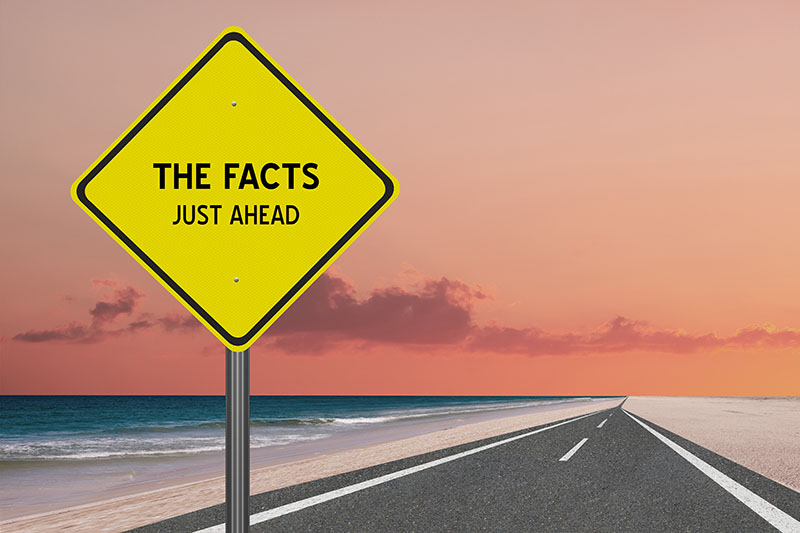
1. Expensive
A recuperator is an additional cost to your spray booth. You can think of it as a “band-aid” to patch up the flaws of a system that requires such an excessive amount of thermal power to begin with. Not only will it be an important initial investment for the material, but it will also substantially add to your installation and maintenance costs.
2. High maintenance
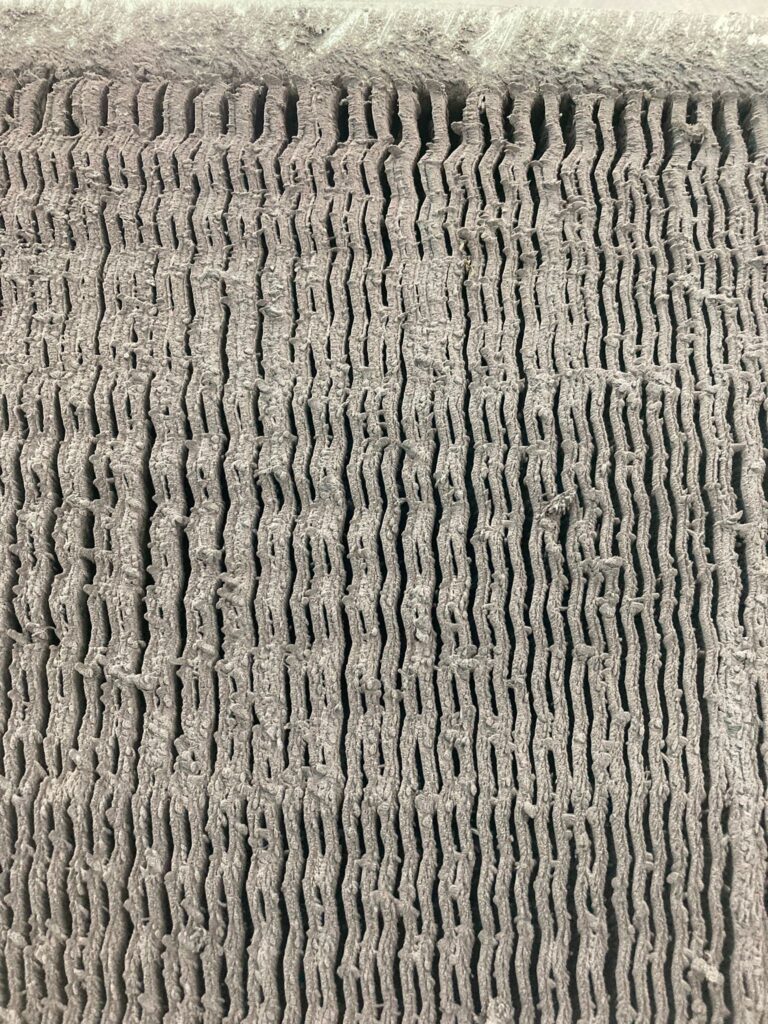
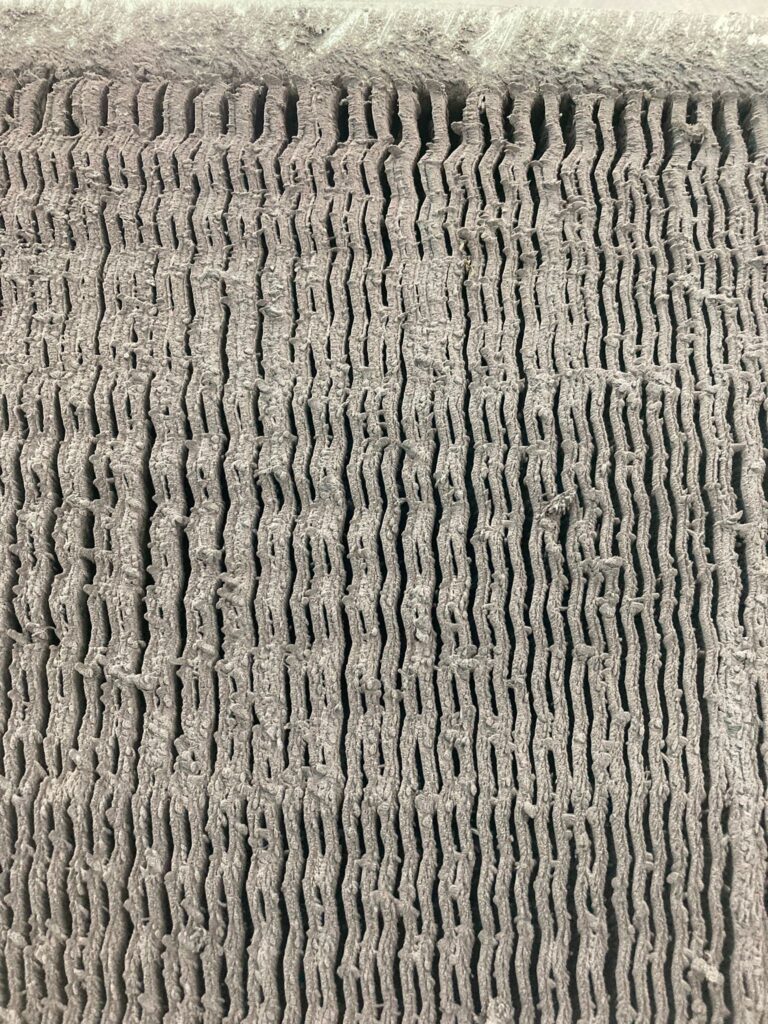
Despite marketing claims, heat recuperators used in spray booths are extremely maintenance intensive. They must be cleaned frequently in order to maintain their original level of efficiency, and if not cleaned properly and on a regular basis, they will likely have to be replaced after just 2 – 3 years of operation. In fact, recuperators are designed for residential purposes, not heavy industrial applications.
3. Problems during the summer months
There is no “off” button, the same system that “saves” energy during the winter will unnecessarily apply to the hot months. During the summer, the air inside the booth will take much longer to cool down after the cure phase. The hot air will mix with the cooler air that is entering the booth. Given that the air entering will likely already be hot, it will take much longer for the booth to cool back down to a decent workable temperature. Time is money my friends!
The common solution for this problem is to add another band-aid: a by-pass. Besides being an additional expensive cost, to install a by-pass takes up a lot of space on top of the space already occupied by the recuperator. This is not counting the extra dampers, servo motors, etc. that will be required to control the by-pass.
4. Recuperators will reduce the performance of the spray booth
Adding a heat recuperator will reduce the overall pressure of the air entering the booth. This will lower the velocity (m/s) at which the air comes down onto the painted objects and therefore the quality and efficiency of the paint job.
In order to compensate for the pressure loss and achieve the desired air velocity, you will have to increase the power of the motors and therefore electric power usage, adding on to the already excessive operating costs of the booth.
Solution
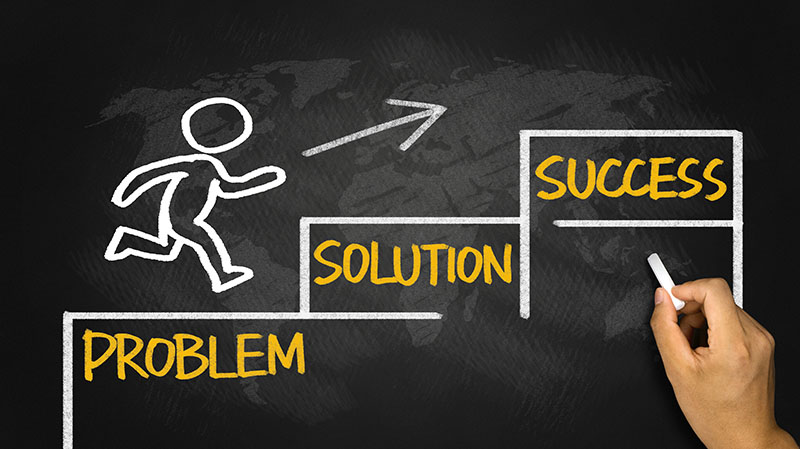
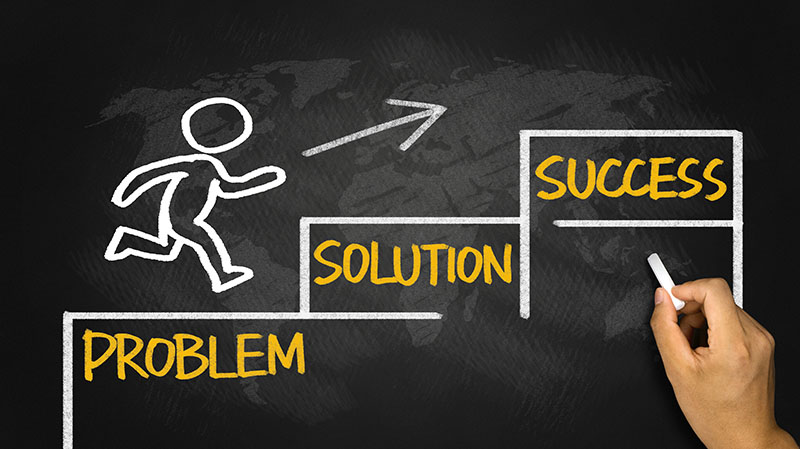
Don’t worry, we’re not here to rain on your parade and point out problems, we provide solutions! Real, affordable, practical solutions designed for the long term not just for the sale.
Our Saicozero Multizones require no burners or electric heating systems to reach 20°C year-round. Depending if the paint you use requires high temperatures or not, they can literally cut your heating costs by 80% or by 100% (THAT MEANS ZERO HEATING COSTS YEAR-ROUND).
No reduced air velocity, no additional costs, no band-aids, that’s just how the system works! A system that our clients have been benefitting from since 2004.
Always two steps ahead in technology
The #Saicozero team